99% der produzierten Kunststoffe basieren auf Erdöl, Flüssiggas oder Kohle (Azoulay et al. 2019, 6 & 11; CIEL 2017, 1). Dafür werden vier bis acht Prozent der weltweiten Öl- und Gasproduktion verwendet (Verrips et al. 2019, 45).
Die aktuell vorherrschenden und dominierenden Produktionsstrukturen der Industrie zur Verarbeitung von Kunststoffen inkl. des konsumierenden Sektors und der Abfallindustrie, basieren auf einem linear strukturierten Wertschöpfungsmodell. Dieses wird von verschiedenen Autoren mit den Worten `take-make-dispose´ (Ellen MacArthur Foundation 2019a, 6; Crippa et al. 2019, 164), `take-make-use-dispose´ (Barra et al. 2018, 3), `take-make-throw´ (Williams et al. 2019, 65), `take-make-waste´ (Lacy & Rutqvist 2015, 4), `extract-produce-use-dump´ (Korhonen et al. 2018, 37) oder sogar als `burn, bury, befoul´-Modell (Forrest et al. 2019, 2) beschrieben.
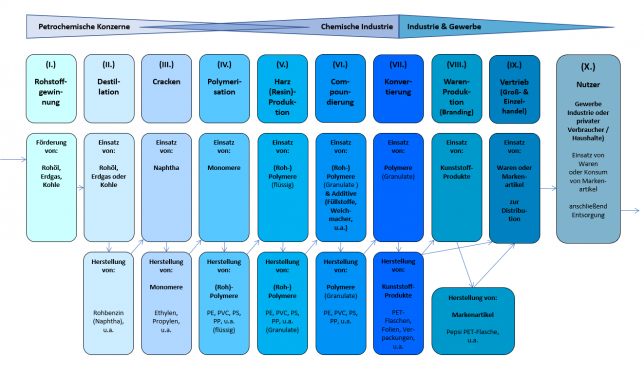
Von der Rohstoffgewinnung bis zur Entsorgung besteht dieses Modell aus zehn Produktions- bzw. Verarbeitungsschritten:
Nach der Rohstoffgewinnung (I.) findet in Raffinerien der Erdöl verarbeitenden Konzerne zunächst die Destillation des zuvor geförderten Erdöls und der Flüssiggase oder die Verarbeitung von Kohle in Rohbenzin statt (II.).
Das Rohbenzin, auch Naphtha genannt, wird in einem anschließenden Prozessschritt (III.) in monomere Grundbausteine wie Ethen oder Buten zerlegt. Dieser Schritt wird auch als `cracken´ bezeichnet. Monomere sind minimal kurzkettige Kohlenstoff-Wasserstoff-Verbindungen, die anschließend (IV.) zu definierten, langkettigen Kohlenstoff-Wasserstoff-Verbindungen polymerisiert werden. Diese Zwischenprodukte besitzen bereits die chemische (Roh-)Polymerstruktur des zukünftigen Endprodukts.
Um die (Roh-)Polymere weiterverarbeiten zu können, werden sie im Schritt (V.) in feste Granulate (Kunststoffharze bzw. Resine) überführt. Diese Resine sind zunächst chemisch identisch mit den (Roh-)Polymeren und die Grundlage für den Verarbeitungsschritt (VI.), das `Compounding´. Bei diesem werden die Resine über mechanisch-thermische Mischvorgänge (Extruder u.a.) mit unterschiedlichen Additiven vermischt. Erst ab dieser Verarbeitungsstufe erfüllen die so erzeugten Polymere chemisch alle Anforderungen an das zukünftige Produkt.
Im Schritt (VII.) wird das Compound in ein Kunststoff-Zwischenprodukt (z.B. Verpackungsfolien, PET-Flaschen, u.v.m.) konvertiert, das den Eigenschaften und der Form entspricht, wie es der Waren- bzw. Produkthersteller benötigt. 36% der Kunststoffproduktion weltweit sind Verpackungsmaterialien bzw. single-used plastics (UNEP 2018, 4). Um als solche genutzt werden zu können, müssen die Zwischenprodukte mit einem Firmenbranding gelabelt (VIII.) und dem Konsumenten über den Groß- und Einzelhandel angeboten werden. Dieser achte Schritt zum Labeling fällt für Kunststoffprodukte weg, die den Konsumenten nicht direkt ansprechen sollen (z.B.: `White-Label´-Kunststoffprodukte für die Automobilbranche oder das Baugewerbe).
Im Anschluss gehen die Produkte über die Logistik an den Groß- und Einzelhandel (IX.) und werden anschließend an den Endkunden verkauft. Dieser nutzt die Artikel und wirft sie weg sofern er diese nicht anderweitig veräußern kann (X.).
Literatur (sofern nicht direkt verlinkt)
mit letztem Zugriff am 25.11.2020:
- Lacy, P. & Rutqvist, J. (2015): Waste to Wealth. London: Palgrave Macmillan UK; DOI: 10.1057/9781137530707